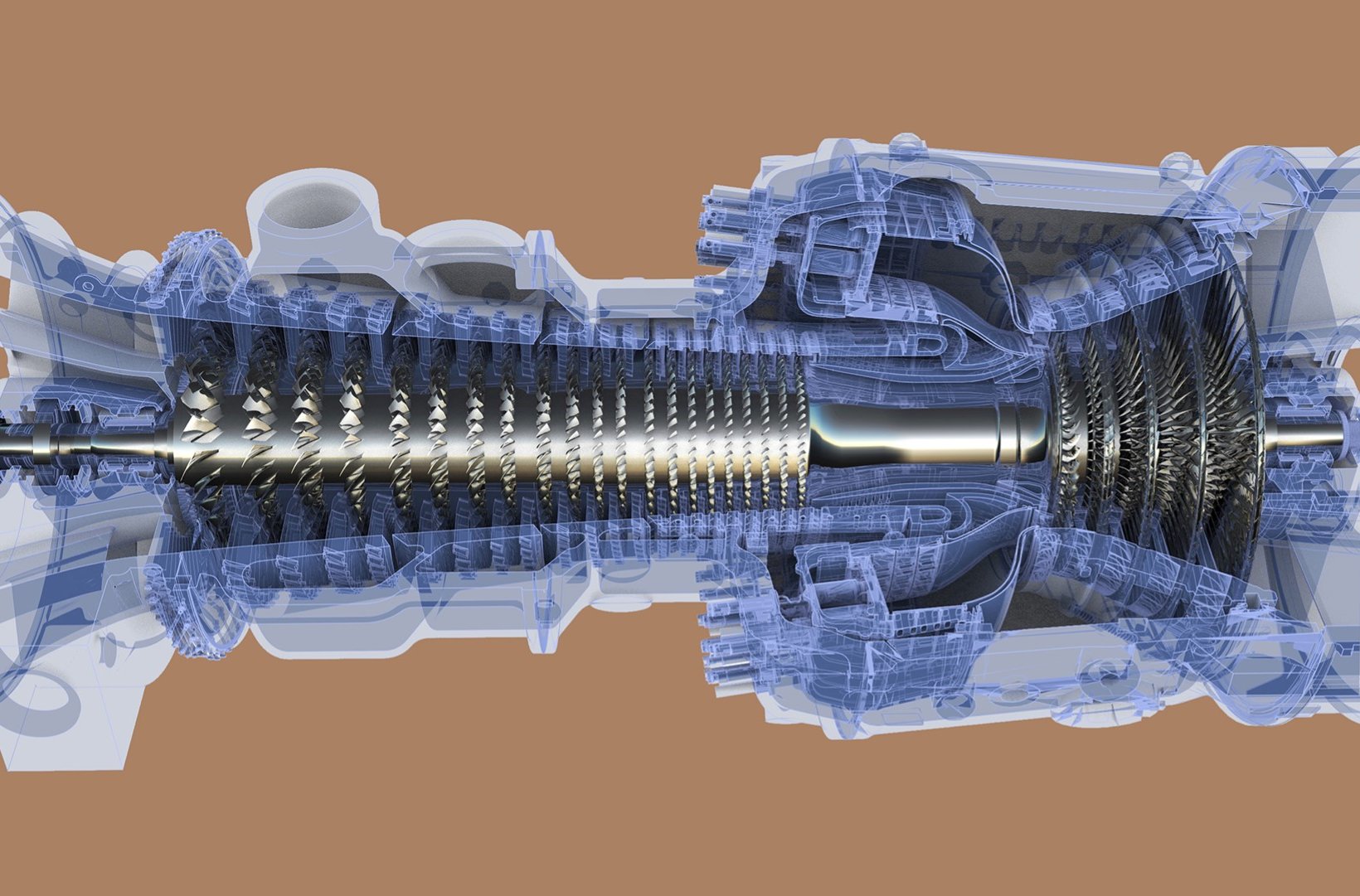
3D-Druck-Bauteile kommen im Heizkraftwerk Mitte zum Einsatz
Das 3D-Druck-Verfahren von Industriebauteilen ist schnell und kostengünstig. General Electric stellt damit per Laserstrahl und Pulver Metallbauteile her. Diese kommen bei Vattenfall im Heizkraftwerk Mitte zum Einsatz. Das Fertigungsverfahren wird auch als selektives Laserschmelzen bezeichnet, auf Englisch: Selective Laser Melting. Hierbei werden räumliche Gebilde schichtweise aufgebaut.
Im Berliner Heizkraftwerk Mitte sind derzeit im laufenden Gasturbinenbetrieb 3D-gedruckte Bauteile in einem Stresstest eingesetzt. Angefertigt hat diese General Electric (GE). Eine der Komponenten, die sich gegenwärtig im Test befinden, gehört zu den weltweit größten Bauteilen dieser Herstellungsart.
Heizkraftwerk Mitte stellt Testfeld im laufenden Betrieb
Dr.-Ing. Harald Kissel, Senior Product Manager bei General Electric berichtet: „Wir sind stolz auf unsere Produkte, die durch Selective Laser Melting (SLM) entstanden sind.“ Dabei produzieren 3D-Drucker auf Basis von Computerdaten dreidimensionale Industriekomponenten per Laser und Pulver. „Besonders hilfreich ist für uns, dass uns mit dem Heizkraftwerk Mitte im Großbetrieb ein Testfeld zur Verfügung steht.“
Mögliche Einsatzbereiche von SLM-Komponenten im Heißgasweg von Gasturbinen
Seit fast zwei Jahren testen GE und Vattenfall einen Prototyp im laufenden Betrieb. Drei weitere Bauteile befinden sich seit 2016 zu Testzwecken in der Gasturbine. Sie werden in regelmäßigen Abständen überprüft. „Dass wir Teil der Bewegung sind, freut uns“, versichert Dietmar Kodim. Er ist Ingenieur bei Vattenfall und verantwortet die Tests und Einsätze der SLM-Komponenten im Heizkraftwerk.
„Mit diesen Feldtests betreten wir Neuland und es macht Spaß, daran mitzuwirken. Wir erhoffen uns von den 3D-gefertigten Komponenten eine Effizienz-Steigerung der Anlage mit einer messbaren Brennstoff-Ersparnis. Wie groß jedoch die Einsparungen letztendlich sind, werden die Ergebnisse des derzeitigen Testlaufs zeigen“, so Dietmar Kodim weiter.
So funktioniert Selective Laser Melting
Ausgangsbasis ist ein präzises digitales 3D-Modell. Der Drucker arbeitet in abgeschlossener Atmosphäre unter Schutzgas. Eine Substratplatte dient als Bauplattform, auf der eine hauchdünne Pulverschicht verteilt wird. Anschließend zeichnet ein Laser die Konturen des Bauteils in das Pulver. Das durch den Laser punktuell aufgeschmolzene Pulver erstarrt.
Das Prinzip des Selective Laser Melting (SLM), Quelle: General Electric Companie
So wird Ebene für Ebene die fertige Kontur des herzustellenden Bauteils gebildet. Nach jedem Durchgang senkt sich die Substratplatte geringfügig ab und neues Pulver wird ausgeteilt. Dadurch entsteht die jeweils nächste Bearbeitungsebene. Dieser Prozess wiederholt sich, bis das Modul komplett ist. Abschließend wird das überschüssige Pulver abgesaugt. Die im selektiven Schmelzprozess hergestellten Konturen bilden so das fertige Bauteil.
Die Konturen sind Zehntelmillimeter genau und der Laser kann Feinstkonturen erstellen. Insgesamt sind Komponenten bis zu einer Bauhöhe von 350 Millimetern und Abmaßen von etwa 250 x 250 Millimetern im SLM-Verfahren herstellbar.
3D-Druck überzeugt durch große Materialvielfalt: Sowohl stabiles Titan, als auch leichtes Aluminium oder elastisches Chrom-Kobalt können verarbeitet werden. Feinstkonturierte Teile sind herstellbar, wodurch sich SLM besonders für den Einsatz in Industrie und in der Fahrzeug- und Flugzeugbranche eignet.
Selective Laser Melting mit Zukunftsmusik
Bauteile, die per SLM-Verfahren entstehen, bieten viele Vorteile. Dennoch sind derzeit, zumindest in Vattenfall Kraftwerken keine weiteren Einsätze geplant. Harald Kissel von GE beschreibt seine Erfahrungen aus der Praxis: „Die Prozesse für die Stresstests sind lang: Nachdem wir den Fertigungsprozess entwickelt und optimiert haben, ermitteln wir die Materialdaten“, berichtet er. Das könne durchaus drei Jahre dauern.
Währenddessen erarbeiten die GE-Experten bereits die Designs für die Bauteile der nächsten Generation. „In unseren Testmaschinen und auf dem Prüfstand checken wir dann, ob die dreidimensionalen Bauteile einwandfrei arbeiten. Erst, wenn alle Versuche erfolgreich waren, folgt der Großfeldtest beim Kunden“, weiß der GE-Ingenieur.
Über kurz oder lang erfährt die 3D-Druck-Methode für Industriebauteile zunehmend Verbreitung. Vor allem gegenüber der Serienproduktion von Teilen. Schließlich entfallen beim 3D-Formgebungsverfahren das aufwendige Herstellen und Wechseln von Formen. Selective Laser Melting ist ein Trend, den die Kooperationspartner GE und Vattenfall weiterverfolgen wollen.
Wikipedia erklärt selektives Laserschmelzen
General Electric veröffentlicht Kooperation mit Vattenfall