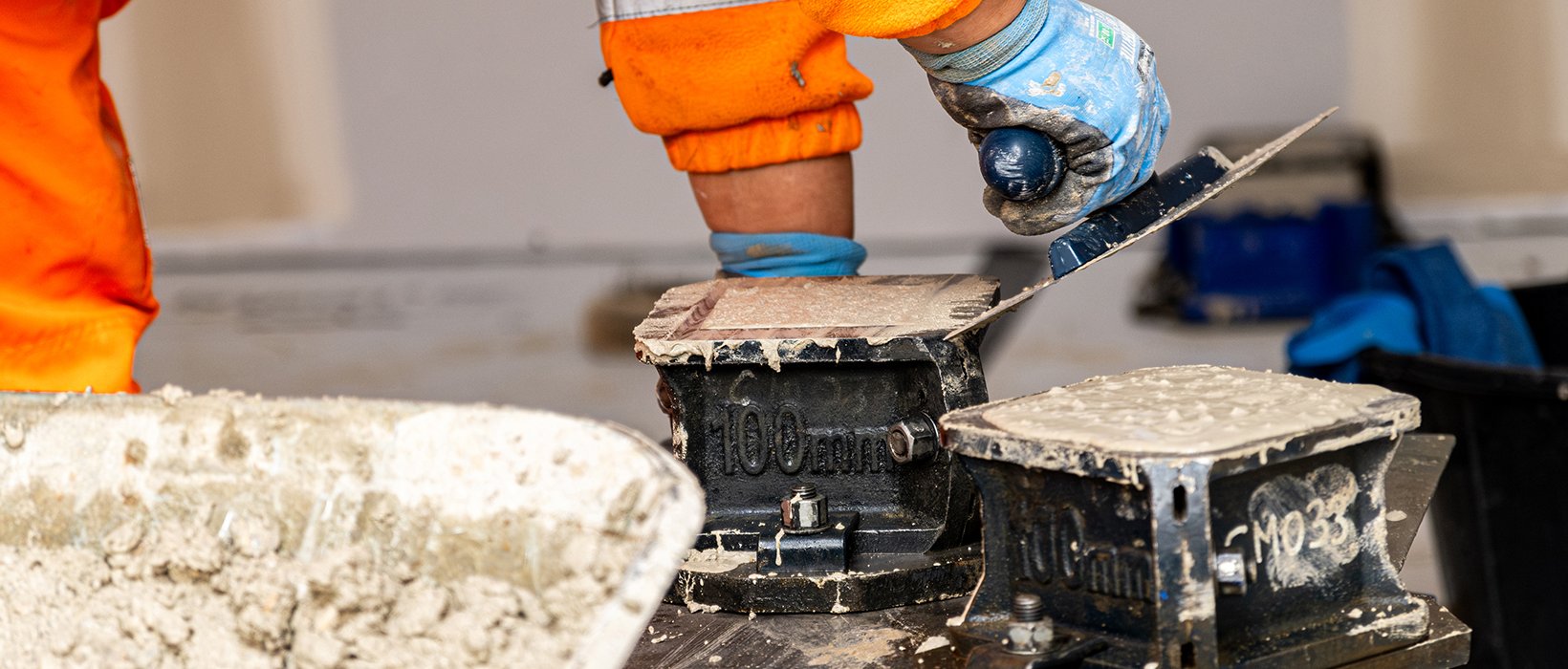
Erprobung der Zukunft von „Nahe-Null“-Zement
Auf Zement entfallen derzeit acht Prozent der weltweiten Kohlendioxidemissionen – angesichts der Forschung und der Fortschritte in der Branche wird sich dies jedoch bald ändern. In Vattenfalls Labor im schwedischen Älvkarleby wird intensiv untersucht, wie sich Zement mit extrem niedrigem CO2-Fußabdruck herstellen lässt, der genauso leistungsfähig ist wie „herkömmlicher“ Zement. Im Moment sieht es so aus, als ob der Bau von Windturbinen mit Zement, dessen Emissionswerte bei nahezu null liegen, schon bald keine Zukunftsmusik mehr ist.
In der kleinen Gemeinde Älvkarleby im Norden der Provinz Uppland ist nicht nur wunderschöne Natur und ein sehr bekannter Wasserfall zu finden, sondern auch eines der ältesten Wasserkraftwerke Schwedens. Zudem befindet sich hier das Vattenfall Labor, in dem in Bereichen von Biodiversität über intelligente Elektrifizierung bis hin zur Entwicklung von Materialien mit möglichst geringem CO2-Fußabdruck geforscht wird.
Das Labor gibt es seit über 80 Jahren. Sein Tätigkeitsgebiet war zunächst hauptsächlich die Sicherheit von Wasserkraftwerken und Staudämmen. Seit den späten 1980er-Jahren hat sich das Geschäftsfeld erweitert. Auf dem Gelände befindet sich heute ein zu Forschungszwecken errichtetes Betonlabor.
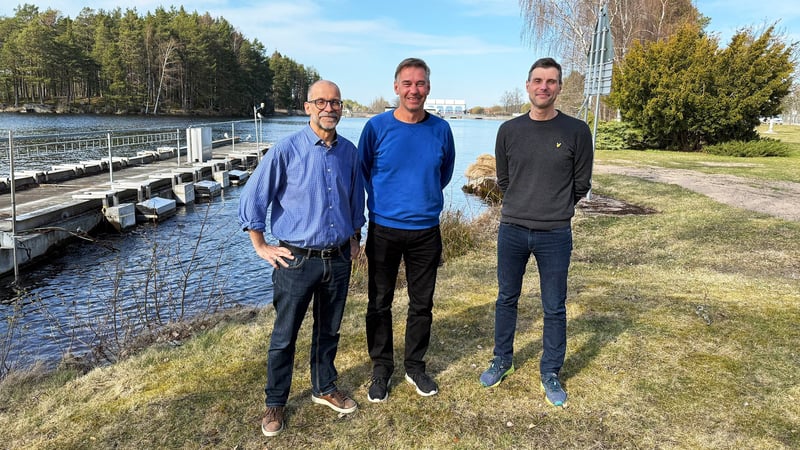
Erik Nordström, Per-Erik Thorsell und Bojan Stojanovic (v. l.) arbeiten im Forschungs- und Entwicklungszentrum von Vattenfall in Älvkarleby. Auf dem Dock hinter ihnen befinden sich Betonproben im Wasser, die darauf getestet werden, wie sie im Zeitverlauf reagieren.
Ursprünglich wurde die Forschung nur für den internen Gebrauch durchgeführt, inzwischen erfolgen dort jedoch auch externe Betontests. Aller Beton, der in großen Infrastrukturprojekten in Schweden verbaut worden ist, wurde zuvor in diesem Labor getestet.
Erik Nordström, Spezialist für Damm- und Wasserbau und Lehrbeauftragter für Betonbau an der KTH, sagt: „Unser Betrieb steht seit Langem beispielhaft für ein Labor mit hochqualifizierten, sachkundigen Beschäftigten und folglich einer Forschung, deren Ergebnisse vertrauenswürdig sind. Im Wasserbau liegt bei uns ein großer Schwerpunkt auf der Instandhaltung unserer Anlagen, damit sie so lange wie möglich halten. Deshalb müssen wir unter anderem verstehen, was Langlebigkeit bedeutet, und wissen, wie wir den Zustand beurteilen und die Bauten instand setzen können.“
Zement, Stahl und Meeresboden
Der Bereich Research & Development bei Vattenfall befasst sich vor allem mit Fragen der Materialauswahl und wie Kohlendioxidemissionen im Rahmen der Geschäftstätigkeit radikal reduziert werden können. Lange Zeit konzentrierte sich die Forschung vor allem auf Zement und Themen wie Fußabdruck, Festigkeit und Langlebigkeit. Vor fünf Jahren wurde dann damit begonnen, auch Stahl zu testen.
Stahl ist für Vattenfall angesichts der großen Türme für Offshore-Windkraftanlagen, die in den Meeresboden gerammt werden, relevant. Vor einigen Jahren wurde aufgrund des wachsenden Interesses, den Meeresboden für die Zwecke der Offshore-Windenergie zu untersuchen, auch ein geotechnisches Labor eingerichtet.
„Die Stärke unseres Labors liegt darin, dass das Wissen Vattenfall-intern vorhanden ist. Wir wollen kompetente Auftraggeber sein und das erfordert Wissen“, erklärt Per-Erik Thorsell, Abteilungsleiter und Leiter des Materiallabors in Älvkarleby.
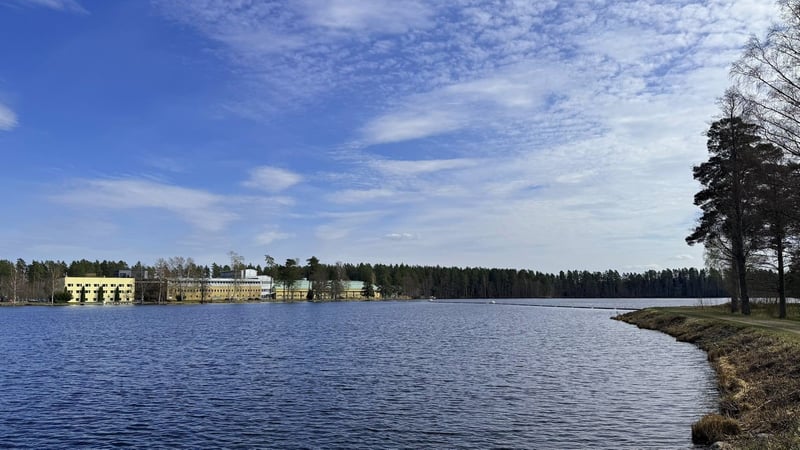
Vattenfall Research & Development liegt in Älvkarleby direkt am Fluss
In der Forschungs- und Entwicklungsabteilung von Vattenfall arbeiten rund 120 Personen, von denen etwas mehr als die Hälfte in Älvkarleby tätig ist. Zement ist das Material, das in Älvkarleby am gründlichsten erforscht wird, und das Ziel ist es, den CO2-Fußabdruck bei der Zementherstellung auf nahezu null zu reduzieren, ohne Abstriche bei der Qualität.
„Beton muss für Bauarbeiten verwendbar sein, bestimmte Leistungsmerkmale aufweisen und stark genug sein, um Lasten über viele Jahrzehnte, vielleicht Jahrhunderte, zu tragen. Jetzt, da wir neue Betonmaterialien entwickeln, müssen wir die Wasserkraft und andere Energiesektoren mit Leitlinien für ihre Anlagen unterstützen“, so Erik Nordström.
Stärkere Nachfrage aufgrund der Zementkrise
Auf Zement entfallen derzeit acht Prozent der weltweiten Kohlendioxidemissionen und er wirkt sich damit erheblich auf das Klima aus. Die Nachfrage nach einer Alternative zu traditionellem Zement, auch Portland-Zement genannt, begann vor etwa fünf Jahren, erklärt Erik Nordström. „Dies ist zum Teil auf verschiedene Vereinbarungen über fossilfreie Infrastruktursektoren und auch auf regulatorische Vorgaben, unter anderem für Zement, zurückzuführen. Ein weiterer treibender Faktor war die Krise der Zementproduktion auf Gotland, die zu der Frage führte, welche Alternativen gäbe es?“
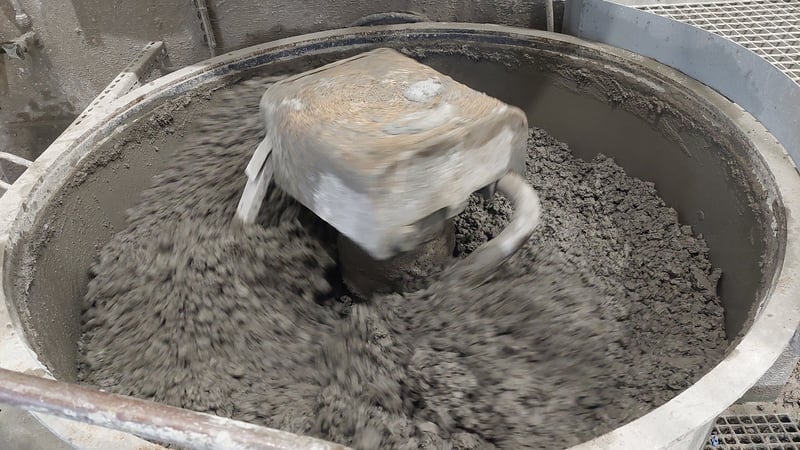
Betonherstellung
Die Lage auf der schwedischen Insel Gotland, die eine kritische Abhängigkeit vom Kalksteinabbau für die Zementproduktion offenbarte, verschärfte sich, als Cementa, jetzt Heidelberg Cement, 2021 die Verlängerung ihrer Betriebsgenehmigung für diese Tätigkeit versagt wurde. Seither gab es diesbezüglich zahlreiche Rechtsstreitigkeiten, die zu einer Verunsicherung der traditionellen Portland-Zementproduktion in Schweden führten.
Bojan Stojanovic, leitender Forschungs- und Entwicklungsingenieur für Baustoffe und Energietechnik im Forschungszentrum in Älvkarleby, hat sich in den letzten Jahren auf Bindemittel für klimagerechten Beton spezialisiert.
Dazu gehört, verschiedene Arten von Zement und Bindemitteln mit niedrigen CO2-Emissionswerten sowie ihre allgemeine Funktion und Anwendung zu untersuchen und zu kartieren. Es ist klar, dass zahlreiche Nebenprodukte aus dem Bergbau und der Stahlindustrie, so genannte Schlacken, zu den zentralen Bestandteilen von Bindemitteln mit niedrigem CO2-Fußabdruck gehören.
Radikal neu versus „harte Realität“
Um den Weg zur Verringerung des Kohlendioxids im Zement über die Zeit zu schildern, zieht Bojan Stojanovic den Vergleich mit einer „Totalreform“. „Am Anfang wurde progressiv und radikal gedacht, aber je weiter wir kommen, desto mehr sehen wir uns mit der „harten Realität“ konfrontiert und müssen uns einige Fragen aus der Langzeitperspektive stellen.
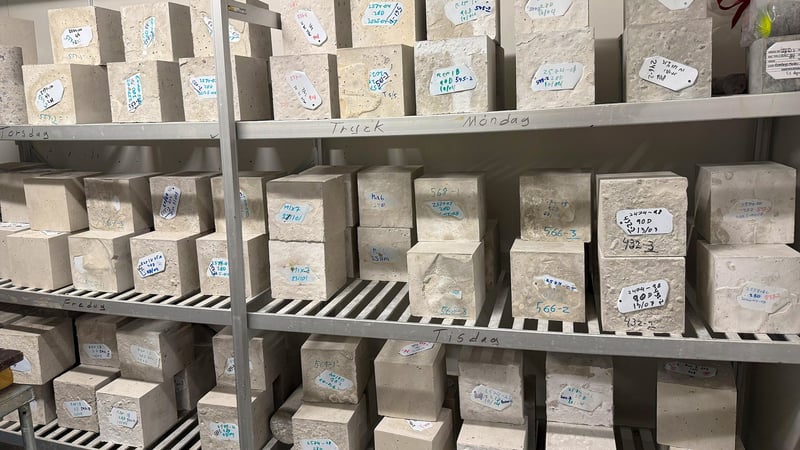
Eins der vielen Regale mit Betonproben im Labor in Älvkarleby.
Fragen wie: Wer kann ein brauchbares Material tatsächlich und in ausreichenden Mengen herstellen, wer kann einen realen und sinnvollen großindustriellen Herstellungsprozess etablieren und realisieren? Wer hat Zugang zu den benötigten Rohstoffen? Wenn wir heute eine Bestellung aufgeben, heißt das, dass wir morgen etwas erhalten?“, erläutert Bojan Stojanovic und fährt fort:
„Wir sind nicht mehr in der Phase, in der wir uns alle Optionen ansehen, sondern wir prüfen, was wir tatsächlich nutzen und erhalten können. Ich würde sagen, dass wir unser Ziel noch nicht erreicht haben, aber etwas mehr als die Hälfte des Wegs geschafft ist, um traditionellen Zement vollständig durch Zement mit geringem CO2-Fußabdruck ersetzen zu können.
Schlackenprodukte in der Zementherstellung sind nicht neu, sondern diese Praxis existiert bereits seit Jahrzehnten. Der Hauptunterschied besteht darin, dass es damals vor allem darum ging, die Kosten zu senken, und nicht wie heute um den CO2-Fußabdruck.
„Es wurde alles Mögliche hineingemischt, zum Beispiel Nebenprodukte aus der Stahlindustrie. Aber aufgrund mangelnder Kenntnisse wurde einfach alles gemischt, und dann traten Probleme mit der Langlebigkeit auf. Einiges funktionierte gut, anderes erwies sich als schlecht“, erklärt Per-Erik Thorsell und betont, wie wichtig es ist, neue Materialien gründlich zu testen und zu erforschen, bevor sie zur Herstellung genutzt werden.
Zement – das Bindemittel im Beton
- Beton besteht zu etwa zwei Dritteln aus Zuschlagstoffen. Dabei handelt es sich um eine Mischung aus Sand, Kies oder Schotter.
- Der Zuschlagstoff wird mit Zement in Pulverform und Wasser gebunden. Dies geschieht durch eine chemische Reaktion, die Hydratation genannt wird.
- Um dem Beton die gewünschten Eigenschaften zu verleihen, werden oft geringe Mengen an Zusatzmitteln zugesetzt. Zusatzmittel können zum Beispiel dafür sorgen, dass der Beton schneller oder langsamer aushärtet oder frostbeständig wird.
- Herkömmlicher Beton besteht aus einer relativ geringen Menge Zement und trägt dennoch den größten Teil zum CO2-Fußabdruck bei.
Zugang zu akkreditierten Labors und Fachwissen entscheidend
Zur Entwicklung von Zement mit niedrigem CO2-Fußabdruck – dem Material, das als Bindemittel im Beton dient, – testet das Labor von Vattenfall verschiedene Konzepte mehrerer Zementhersteller. Einer davon ist der schwedische Zementhersteller Cemvision.
„Für uns war es entscheidend, die Tests hier in Vattenfalls akkreditiertem Labor in Älvkarleby durchzuführen und auf das dort vorhandene Fachwissen zurückzugreifen. Es gibt verschiedene Parameter, auf die der Beton getestet wird, zum Beispiel Langzeitfestigkeit, Frostbeständigkeit, Chloridbeständigkeit und Karbonatisierung, um nur einige zu nennen“, sagt Max Larsson von Reybekiel, Marketingleiter bei Cemvision.
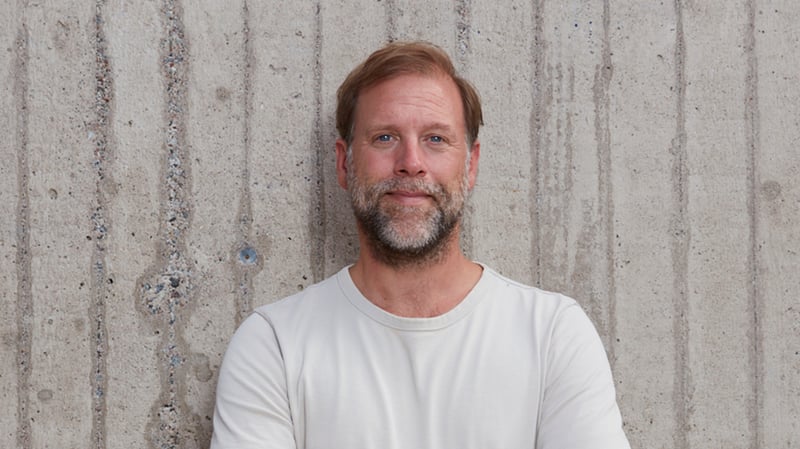
Max Larsson von Reybekiel, CMO Cemvision
Im Juni 2024 unterzeichneten Vattenfall und Cemvision eine Kooperationsvereinbarung über die Entwicklung und künftige Lieferung von Zement mit nahezu null Kohlendioxidemissionen. Die Parteien arbeiten ferner zusammen, um zu zeigen, dass es durchaus möglich ist, herkömmlichen Zement, auch Portland-Zement genannt, durch Zement mit niedrigem CO2-Fußabdruck zu ersetzen. Doch um die Nachfrage ernsthaft anzukurbeln, muss die Normung überarbeitet werden, sagt Max Larsson von Reybekiel.
„Die heutigen Normen sind auf Portland-Zement ausgelegt. Sie sind in der Regel sehr traditionell orientiert und legen fest, welche Rohstoffe enthalten sein dürfen. Das birgt die Gefahr, dass die Tür für innovativere Ansätze verschlossen bleibt. Auf der ganzen Welt wird auf leistungsbezogene Normen umgeschwenkt, was auch in Schweden und der EU der nächste Schritt sein muss.“
Ein weiterer entscheidender Faktor für die Entwicklung von Zement mit extrem niedrigem CO2-Fußabdruck sind wirtschaftliche Anreize.
„Große Emittenten, wie die aktuellen Zementhersteller, erhalten derzeit kostenlose Emissionszuteilungen, die jedoch ab 2026 auslaufen. Das bedeutet, dass sie Steuern auf Emissionen zahlen müssen und bis 2034 werden das 100 Prozent sein. Wenn die Hersteller diese Kosten an die Kunden weitergeben, könnte das bedeuten, dass Zement um das Jahr 2030 herum etwa 300 Prozent teurer wird“, fügt Max Larsson von Reybekiel hinzu.
Wie weit sind wir bei der schrittweisen Abkehr von traditionellem Zement gekommen? Vattenfall hat sich zum Ziel gesetzt, bis 2030 zehn Prozent der gesamten Betonproduktion aus Zement mit nahe null Emissionen herzustellen. Nach dem derzeitigen Kenntnisstand scheint dieses Ziel erreichbar zu sein.
Windkraftanlage im Maßstab 1:1 mit „Nahe-Null“-Zement in Sicht
Im Hof des Betonlabors von Vattenfall in Älvkarleby wird demnächst ein Abschnitt eines Windkraftfundaments gegossen, um nachzuweisen, dass es in industriellem Maßstab gebaut werden kann, erklärt Erik Nordström.
„Wir werden die Eigenschaften des Betons durch Messungen und Probenahmen weiter untersuchen, bevor wir endgültig sagen können, dass er sich für den Bau eines Windparks eignet. Dann wird wahrscheinlich auch nicht gleich ein ganzer Park gebaut werden, sondern erst einmal mit ein paar großen Fundamenten begonnen.“
Windparks an Land haben den Vorteil, dass die Fundamente auch nach etwa 25 Jahren noch ersetzt werden, wenn beispielsweise größere Turbinen gebaut werden. Außerdem sind diese Fundamente nicht so rauen Bedingungen ausgesetzt wie Wasserkraftwerke und Offshore-Windkraftanlagen, was die Windenergie an Land zu einem für den Anfang geeigneten Anwendungsgebiet macht.
„Auf viele mag es so wirken, als ob die Entwicklung nur langsam voranschreitet, aber mit konkreten technischen Vorgaben zu arbeiten, nimmt viel Zeit in Anspruch. Allein die Überprüfung aller Eigenschaften im Labor dauert ein Jahr, die Tests sind also zeitaufwändig“, erklärt Erik Nordström.
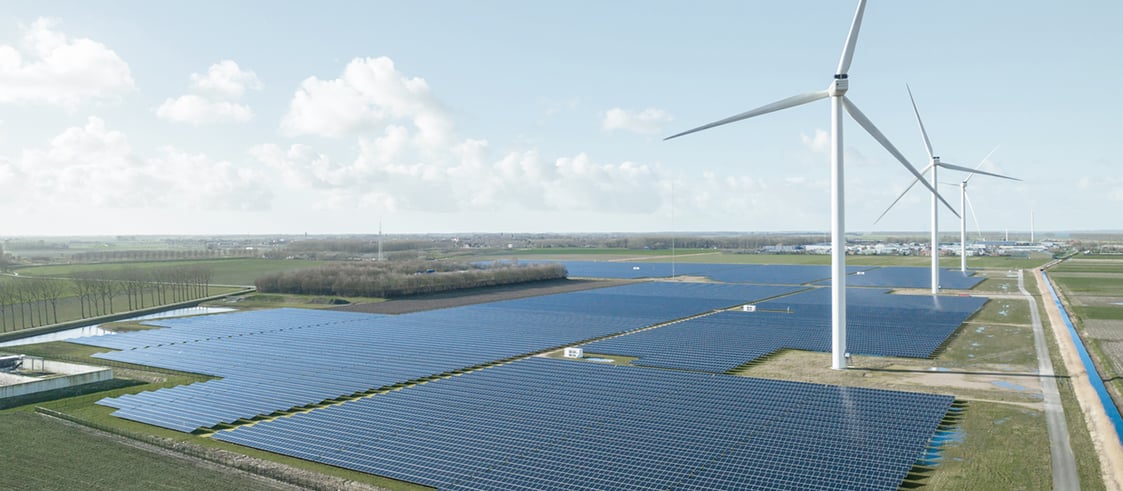
Registrieren Sie sich für unseren Newsletter THE EDIT
THE EDIT ist der neue monatliche Newsletter von Vattenfall. Jede Ausgabe beleuchtet ein neues brennendes Thema aus der Welt der nachhaltigen Energie und der fossilen Freiheit.