Komponenten aus dem 3D-Drucker sichern die Zukunft der Kernkraft
Mit Verlängerung der Betriebsdauer der schwedischen Bestandsreaktoren auf 80 Jahre wird es umso wichtiger, dass Ersatzteile zur Verfügung stehen. Mittels 3D-Druck lassen sich Komponenten herstellen, deren Qualität womöglich sogar noch besser ist als die der Originalteile.
Die additive Fertigung, zumeist als AM abgekürzt, findet immer breitere Anwendung. Mit Hilfe eines 3D-Druckers und einer digitalen Zeichnung werden Komponenten auf die Art hergestellt, dass zum Beispiel Metallpulver Schicht für Schicht aufgetragen wird. Daher auch der Name Additive Fertigung. Jede Schicht wird mittels Lasertechnik aufgeschmolzen, bis schließlich die fertige Komponente entstanden ist.
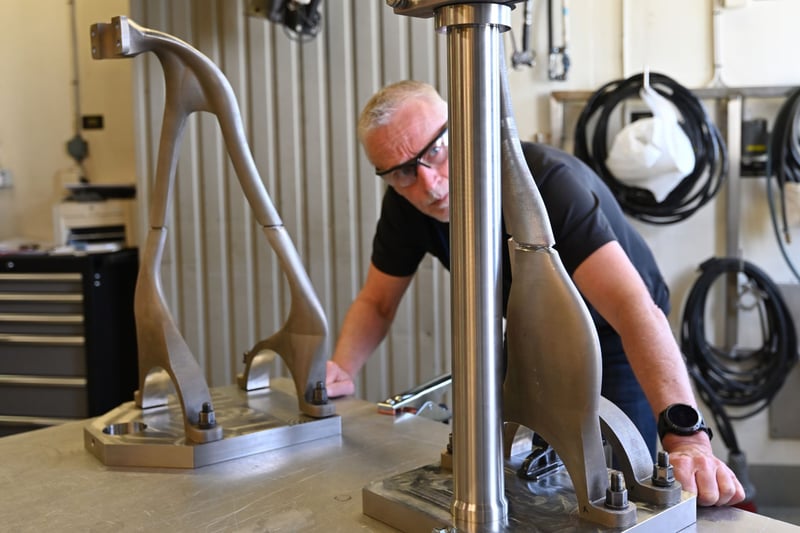
Björn Forssgren, Spezialist für metallische Werkstoffe bei Vattenfall prüft 3D-gedruckte Rohrhalterungen vor der Installation in Ringhals 3.
In der Fertigungsindustrie werden immer mehr Produkte auf diese Weise hergestellt, wie beispielsweise in der Automobil-, Luft- und Raumfahrt- und Verteidigungsindustrie oder in der Medizintechnik, unter anderem passgenaue Hörgeräte, Implantate wie Kugelgelenke für die Hüfte und vieles mehr.
Ersatzteile für die Kernkraft
Die additive Fertigung ist auch eine gute Möglichkeit, Ersatzteile und Komponenten für Kernkraftwerke herzustellen. Schweden verfügt über sechs Kernreaktoren, die alle in den 1970er- und 1980er-Jahren gebaut wurden. Vattenfall gehören fünf dieser Reaktoren und es laufen nun umfangreiche Projekte zur Verlängerung ihrer Betriebsdauer von 60 auf 80 Jahre. Das bedeutet, dass Komponenten in großer Zahl durch neue ersetzt werden müssen. Allerdings ist es schwierig, diese Ersatzteile zu beschaffen und qualifizierte Lieferanten zu finden. Lange Vorlaufzeiten und hohe Kosten können die Folge sein, und im schlimmsten Fall müssten ganze Komponenten ausgetauscht werden, weil keine Ersatzteile verfügbar sind.
Die Ersatzteilverfügbarkeit ist zusätzlich dadurch eingeschränkt, dass einige Großunternehmen Subunternehmen aufgekauft haben, um sich die Lieferketten für ihre eigenen Reaktoren zu sichern.
„Diese Entwicklung bedeutet, dass wir das Risiko sehen, bei der kurzfristigen Beschaffung von Komponenten ins Hintertreffen zu geraten. Durch den Einsatz von AM können wir die Produktion selbst steuern und priorisieren, was letztlich zu einer höheren Verfügbarkeit unserer Erzeugungseinheiten – und damit zu mehr fossilfreier Stromproduktion – beiträgt“, erklärt Björn Forssgren, Spezialist für metallische Werkstoffe im schwedischen Kernkraftwerk Ringhals und dort in der Forschung und Entwicklung für dieses Gebiet zuständig.
Vor diesem Hintergrund beschloss Ringhals bereits 2017, sich zur Finanzierung eines 3D-Druckers mit vier anderen Unternehmen aus der Region zusammenzutun. Die Zusammenarbeit wird von RISE, Research Institutes of Sweden, geleitet. Aktuell sind 21 Unternehmen beteiligt, die unter anderem bei der Technologieentwicklung kollaborieren.
„Wir haben das Potenzial der AM-Technologie früh erkannt, und in vielen Branchen ist sie bereits die neue Normalität. Das Wichtigste für uns ist die unglaubliche Flexibilität der Technologie. Wir können damit so ziemlich alles herstellen: Rohre, Ventile, Pumpengehäuse, Innenteile dafür, und auch bei den Materialien gibt es keine Einschränkungen. Es lassen sich praktisch alle Arten von Legierungen einsetzen“, sagt Björn Forssgren.
Mindestens so gut wie herkömmliche Komponenten
AM ist eine neue Technologie, und ein Großteil der bisherigen Arbeit bestand in der Überprüfung der Fertigung und der Materialien sowie in der sorgfältigen Untersuchung und Prüfung der strukturellen Integrität der Teile aus dem 3D-Drucker, dass heißt ihrer Festigkeit, Haltbarkeit, Widerstandsfähigkeit über die Zeit und so weiter. Und die Ergebnisse sind sehr positiv:
„AM ist ein hochgradig kontrollierter Fertigungsprozess. Alle unsere Studien zeigen, dass die auf diese Weise hergestellten Komponenten mindestens genauso gut sind wie solche, die nach klassischen Verfahren gefertigt werden. Wir haben strikte Anforderungen und nutzen die Technologie, um sicherzustellen, dass die strukturelle Integrität gleich und in vielen Fällen sogar besser als bei herkömmlichen Ersatzteilen ist.“
Heute sind in allen drei schwedischen Kernkraftwerken – Ringhals an der Westküste, Forsmark an der Ostküste nördlich von Stockholm und Oskarshamn, Eigentum von Fortum, im Südosten – AM-gefertigte Komponenten verbaut. Bislang sind das bestimmte Komponenten, die keinem hohen Druck ausgesetzt sind. Es wird jedoch auf internationaler Ebene an der Entwicklung von Normen für die AM-Fertigung unter Druck stehender Teile gearbeitet.
„Wir hoffen, dass es eine solche Norm in naher Zukunft geben wird. Sobald das der Fall ist, können wir uns näher damit befassen, solche Komponenten in unseren Anlagen zu installieren.“
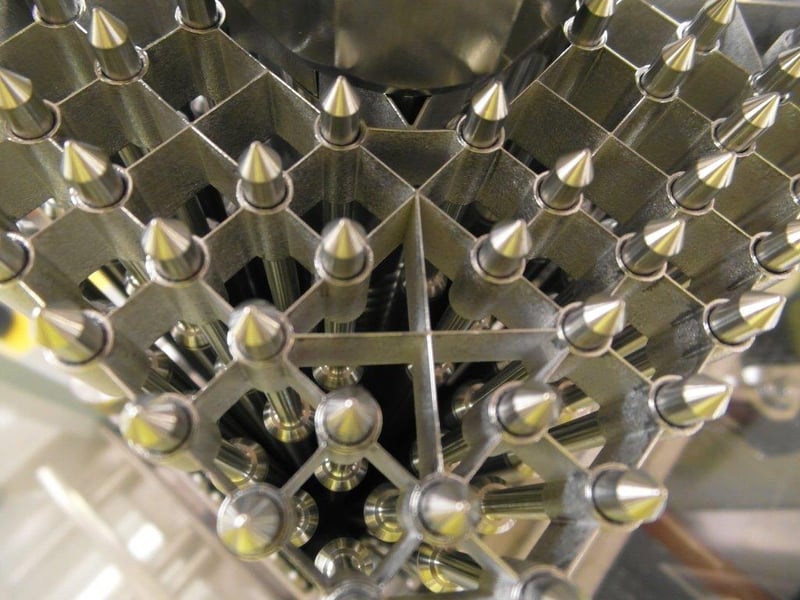
Diese 3D-gedruckte Deckplatte stützt die Brennstäbe in einem Brennelement und ist ein Beispiel für eine AM-gefertigte Komponente, die aktuell in schwedischen Kernkraftwerken verbaut ist.
Der nächste Schritt könnte daher eine unternehmensinterne 3D-Druckanlage sein. Damit könnten andere Kernkraftwerke und sogar andere Arten der Stromerzeugung innerhalb Vattenfalls mit Ersatzteilen versorgt werden. Björn Forssgren fasst zusammen:
„Die Anlagen werden nicht jünger. AM ist ein Instrument, um unsere Verfügbarkeitsziele zu erreichen und das Risiko von Anlagenstopps verringert. In Bezug auf Komponenten, die in dieser Hinsicht als risikoreich gelten, wollen wir proaktiv arbeiten. Wir legen daher virtuelle Lager mit digitalen CAD-Modellen an, damit wir bei Bedarf neue Komponenten in 3D drucken können. Jede geplante Abschaltung ist extrem teuer, beeinträchtigt die Verfügbarkeit und schadet auch dem Vertrauen in die Kernenergie.“
Additive Fertigung
- Bei der AM bzw. beim 3D-Druck stellt ein Drucker Objekte aus digitalen Dateien her. Diese können aus Glas, Kunststoff, Metall oder anderen Materialien, sogar aus Lebensmitteln, gefertigt werden.
- Die Technologie hat viele Vorteile gegenüber Gieß- oder Schmiedetechniken: minimaler Materialabfall, leichtere Erfüllung nuklearspezifischer Legierungsanforderungen, Fertigung von Produkten, die von Lieferanten nicht mehr hergestellt werden, schnelle Produktion mit direkter Lieferung und die Möglichkeit, Zeichnungen digital zu speichern, anstatt physische Teile zu lagern.
- Das Verfahren eröffnet Möglichkeiten zur Verwendung von Materialien nach dem Kreislaufprinzip, da ein ausrangiertes 3D-gedrucktes Metallobjekt zu Pulver recycelt und für den Druck eines neuen Objekts verwendet werden kann.
- Ein moderner 3D-Drucker mit vier Laserquellen kann bis zu 170 Kubikzentimeter Material pro Stunde verarbeiten.
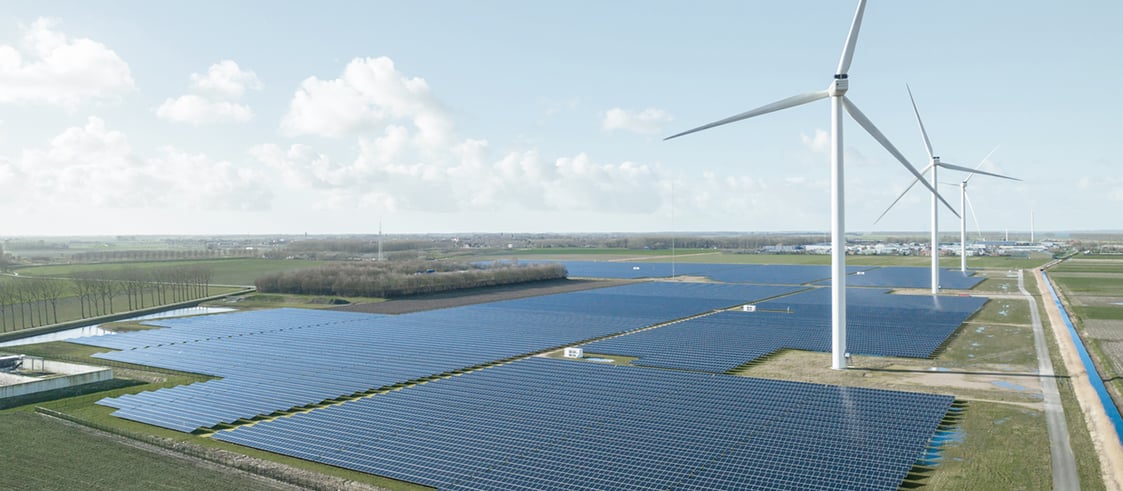
Registrieren Sie sich für unseren Newsletter THE EDIT
THE EDIT ist der neue monatliche Newsletter von Vattenfall. Jede Ausgabe beleuchtet ein neues brennendes Thema aus der Welt der nachhaltigen Energie und der fossilen Freiheit.