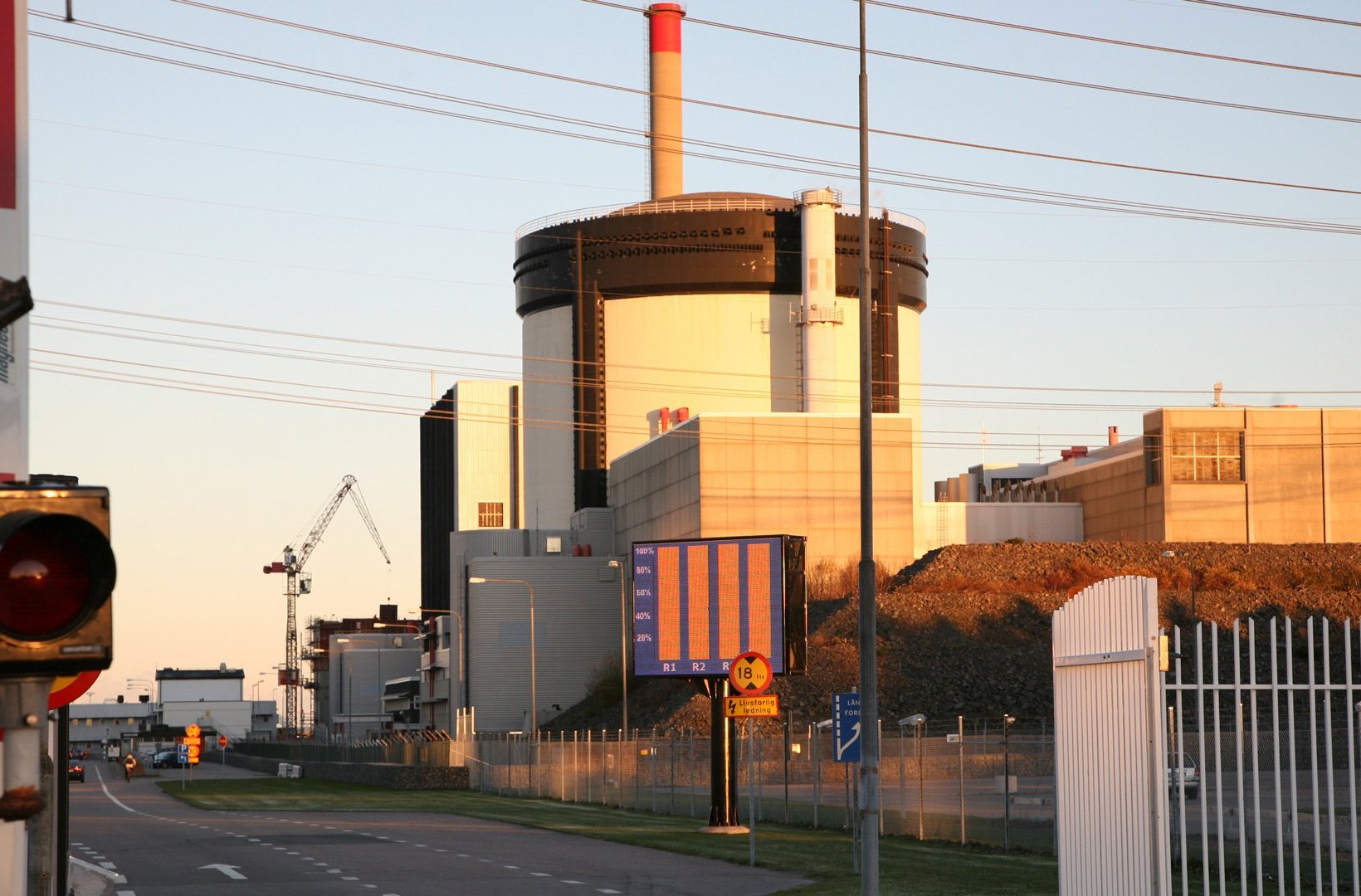
Preem and Vattenfall aim to produce fuel with an insignificant environmental impact through a process that includes hydrogen gas. At Preem's refinery in Gothenburg, the companies are jointly conducting a pilot study for producing hydrogen gas with the help of fossil-free energy. They recently visited Ringhals to see the twenty-year-old hydrogen gas factory.
Though it has been in operation since 1997, Ringhals' hydrogen gas factory has gone largely unnoticed. At the far corner of the industrial area and up a flight of stairs is where you'll find the factory that supplies Ringhals 1 with hydrogen gas.
Same components regardless of size
The electrolyser is the heart of the factory. It is in this that the electrical current passes through water and splits it into hydrogen gas and oxygen. The hydrogen gas is used in Ringhals 1 to cool the generators. It is also injected into the feedwater to prevent corrosion. The oxygen is released into the air.
The Ringhals electrolyser is 0.8 MW and the factory normally produces between 60 and 110 normal cubic metres of hydrogen gas per hour. The factory that Preem and Vattenfall are planning will have an 18 MW electrolyser and a production of approximately 3,800 normal cubic metres of hydrogen gas per hour.
"We are keen on visiting Ringhals, not only to look at the electrolyser but also to gain knowledge about starting up and operating such a factory. Here we can find useful expertise for our project," says Linda Werner, Business Development, Preem.
"The same components are used regardless of the size of the facility. For large facilities, the number and size of the components just have to be larger," says Anders Wik, Head of Nuclear Generation R&D at Vattenfall.
Hydrogen gas production is based on electrolysis. Using an electric current, water molecules are split into their constituent parts: oxygen and hydrogen gas.
The project enables biodiesel
The visit is part of a pilot study for a planned hydrogen gas facility in Gothenburg in which Vattenfall and Preem will be collaborating. For Vattenfall, the project is fully in line with the focus to become fossil-free within a generation.
"We believe that hydrogen gas will become an increasingly important energy source in the future. Not only can it be used in steel manufacturing for the Hybrit project and in Preem's production of biodiesel, but it also has the promise of acting as a buffer in the electrical system," says Anders Wik.
Preem sees the strength in collaborating on this project.
"The rate at which we produce renewable fuels needs to be high and we strive to spearhead technological development. The conditions are all here in Sweden. For example, we have the forest and industrial waste as the basis for our raw materials and our electricity generation is fossil-free. In addition, a common denominator of Vattenfall and Preem is our joint high focus on safety," says Linda Werner.
Facts - Making diesel from conifers and hydrogen gas
Sustainable biodiesel has the same chemical composition and attributes as fossil diesel. It can be produced using lignin, a binding agent from paper and pulp factories which is left behind after the fibres needed for paper-making have been separated out. An important part of the process of converting lignin to diesel is to use hydrogen gas for the oxygen reduction stage. By using lignin, the production of biodiesel can increase many times over compared to current levels.