Artificial intelligence combined with drones offers significant advantages for offshore wind. Advanced AI technologies not only enhance safety and efficiency of offshore activities but also reduce emissions and lower operational costs. AI-equipped drones perform complex inspections, maintenance, and cargo delivery, enabling wind turbines to perform at their peak.
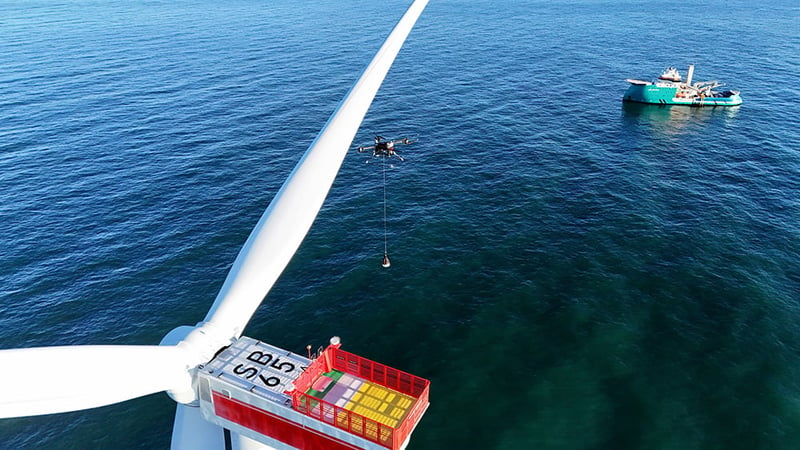
Photo: Ampelmann.
Regulatory compliance
New applications and capacities of drones frequently surpass existing regulations, requiring ongoing adjustments in legislation. For instance, regulations for ‘Beyond Visual Line of Sight’ (BVLOS) operations, where the operator has no direct visual sight of the drone and other airspace users, are evolving. Similarly, autonomous vessels must comply with the regulations set by the International Maritime Organisation (IMO) to guarantee safety and environmental protection.
AI-equipped drones can work independently, find their required flight path and avoid obstacles. Aerial drones are used in Vattenfall's offshore activities for the inspection of wind turbine blades and are being tested for spare part delivery, while unmanned vessels are used for seabed surveys and for the inspection of foundations below the water level. Some drones are piloted by a nearby pilot, while others are piloted by a remote-control center, which can even be located in another country.
Data and images collected by inspection drones are merged and analysed by machine learning algorithms to detect cracks, erosion, dirt, and other anomalies. The data is stored in the cloud, categorised by severity, compared with historical data and finally reports are generated for maintenance teams. This enables proactive maintenance planning, which can prevent major repairs.
Testing drone technologies
By contributing technical expertise, Vattenfall is supporting the AIRTuB-ROMI initiative in the Netherlands, to improve offshore wind maintenance using in-blade monitoring and drone-crawler robots. The project, supported by the Dutch Ministry of Economic Affairs and an industry-academic collaboration, will evaluate three different sensor technologies in turbine blades.
When the sensors detect an anomaly, AI algorithms help to predict the potential damage and its location. A drone-crawler is automatically deployed from its offshore docking station within the wind farm to perform a further inspection.
Tomas Jansen, product manager O&M Automation for Vattenfall Offshore Wind in Germany, explains: "After take-off of the drone, it will autonomously capture high-resolution images of the blades from different angles. The drone will then land on the blade to conduct an ultrasonic scan of the potentially damaged area, giving us complete information of the structural health of the blade. With this detailed information, the maintenance team can initiate repair planning as needed.”
Spare parts delivery
Thanks to advanced sensors and AI-powered software, cargo drones can fly safely in complex offshore environments, avoid obstacles and adapt to changing weather conditions. They can transport materials and equipment from a service operation vessel (SOV) to wind turbines, reducing the need for vessels to go back and forth. The use of an unmanned air vessel (UAV) speeds up the delivery of materials, saves time, and reduces CO2 emissions by eliminating the need for a crew transfer vessel (CTV).
This innovation was recently tested in Vattenfall’s offshore wind farms DanTysk and Sandbank in the German North Sea. A collaboration between offshore service provider Ampelmann, Dutch Applied Scientific Research Institute TNO, and Vattenfall demonstrated the use of cargo drones in the offshore environment.
Video player requires marketing cookies.
To view this content please click here to allow marketing cookies.
Cargo drone test DanTysk and Sandbank. Video: Ampelmann
Roddy Douglas, automation engineer at Vattenfall Offshore Wind in the UK, was involved in the test: “The innovation we showcased included using UAVs for rapid deliveries and pre-loading spare parts and tools to the turbine's nacelle. This is especially beneficial when a part is needed unexpectedly, allowing the on-site team to work efficiently, without waiting for a ship, minimising downtime and revenue loss at wind turbine generators. For sites closer to the coast, cargo can be transported directly from the service center, where operators use automated drones to deliver essential cargo even in challenging weather conditions.”
Underwater inspections and surveys
Uncrewed vessels and remote-controlled drones enhance employee safety during inspections at sea and ensure environmentally friendly operations.
During installation works at offshore wind farm Hollandse Kust Zuid in the Dutch North Sea, Vattenfall deployed 12-meter-long uncrewed surface vessel Blue Essence, equipped with an electrical remotely operated vehicle (eROV) for inspections and seabed mapping. Developed in close collaboration with partner Fugro, this innovation reduces the reliance on crewed vessels, speeds up inspections and minimises environmental impact. The uncrewed vessel with eROV features advanced sensors, sonar, and high-definition cameras that provide real-time data on cable and foundation conditions.
Both the uncrewed vessel and eROV can operate 24/7, withstand wind speeds of up to 38 kilometers per hour (wind force 5), and handle wave heights of up to one and a half meters. They are remotely operated from Fugro's control rooms in Aberdeen, Scotland. As offshore wind projects move further offshore, the advantages of remote-controlled vessels become increasingly significant. Initial operations have shown that uncrewed vessels emit approximately 95 per cent less CO2 compared to traditional survey vessels. Additionally, their smaller size reduces the impact on marine life.
Fit for the future
Upcoming developments in AI are set to significantly improve the capabilities of drones in offshore wind operations. With more advanced AI algorithms, drones could become even more autonomous, capable of making independent decisions during complex inspections and early-stage damage detection without human intervention.
“AI-equipped drones have the potential to free up valuable offshore working time. Given the scarcity of skilled technicians in the offshore wind industry, this is an important advantage. The drones can, for example, perform recurring lightning protection tests on large wind farms, allowing technicians to focus on solving specific issues identified by the drones”, says Tomas Jansen.
Roddy Douglas underscores the positive outcomes of tests in the offshore environment with cargo drones and AI-technology: “The results of our recent demonstrations in our wind farms provide a glimpse into the future of automated and intelligent offshore transport solutions and we have already planned additional tests. In collaboration with our partners, we are dedicated to further exploring promising developments to meet the increasing demand for wind energy, both now and in the future."
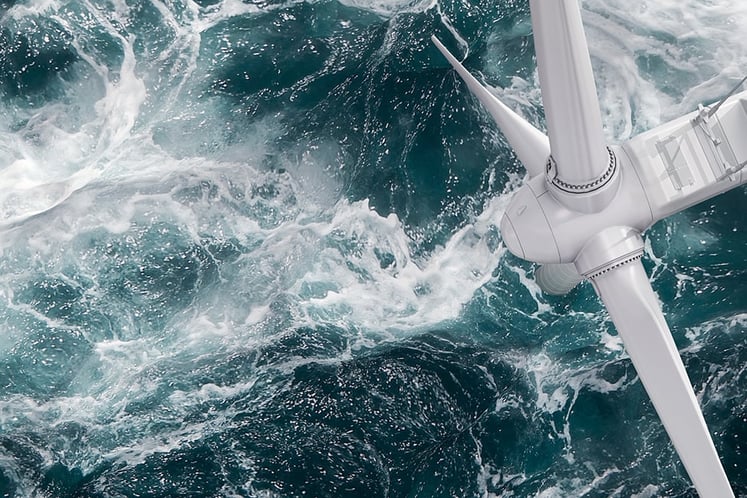
Subscribe to the newsletter THE EDIT
THE EDIT is Vattenfall's new monthly newsletter. Each issue highlights a new burning issue from the world of sustainable energy and fossil freedom.