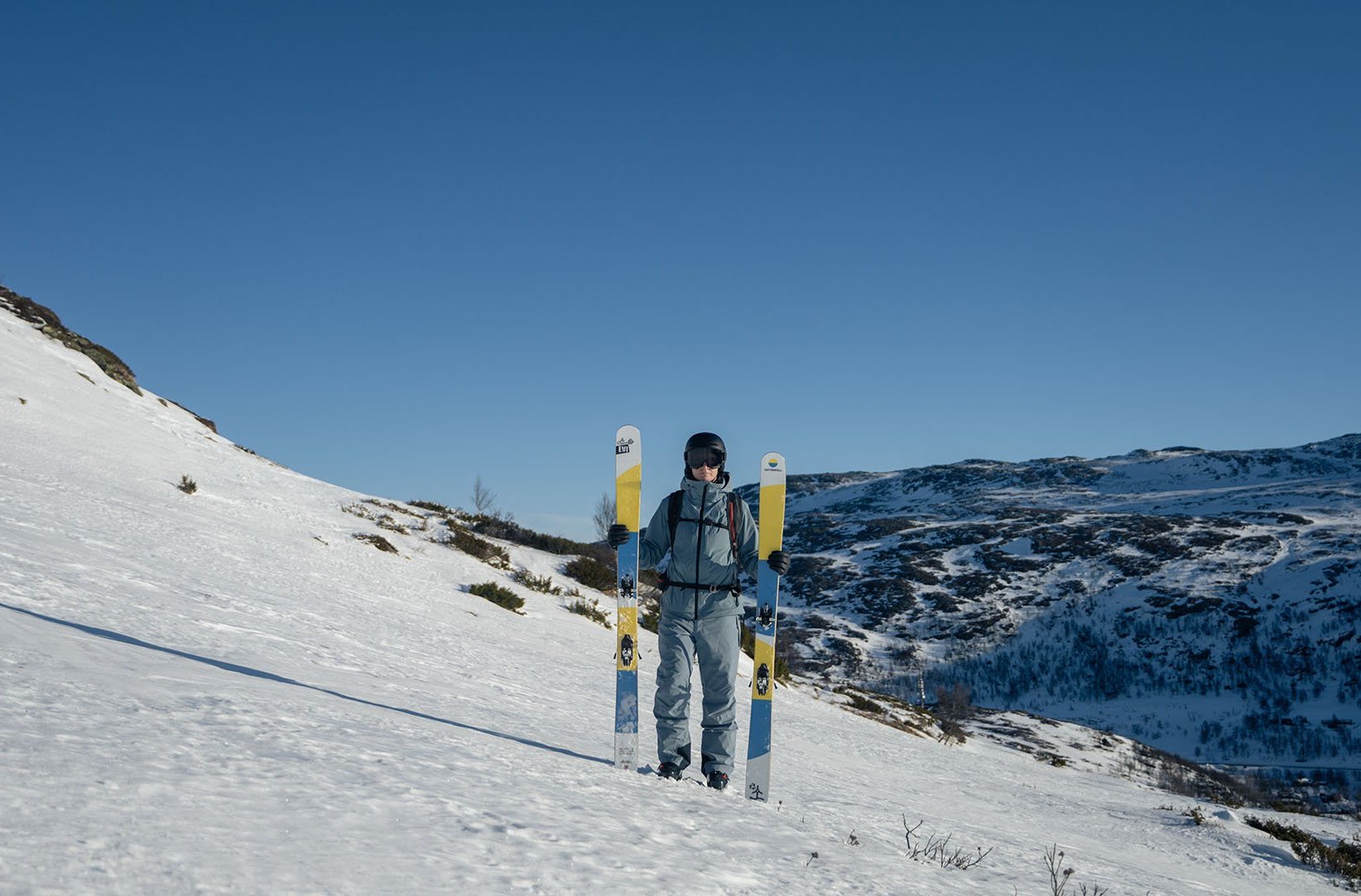
This is how a wind farm became part of a ski
Five years ago, Vattenfall was planning the dismantling of one of its first major wind farms. At the same time, Vattenfall decided to rule out sending the materials to landfill. In the search for alternative ways of working, they quickly found a match with Norwegian recycling company Gjenkraft. Today, the collaboration has resulted in the production of skis using carbon fiber from rotor blades.
According to Gustav Frid, environmental and sustainability specialist at Vattenfall, the search for new methods to handle the enormous amount of composite material found in a wind farm was a natural fit in 2020.
The decision to look for alternative solutions was driven by the concerns expressed in the media about how to deal with this type of waste when several wind farms were nearing the end of their lifespan.
“There was a lot of discussion in the outside world regarding how to handle composite waste. In addition, we had ongoing strategy work, which included a ban on landfilling waste. The goal was to find solutions that were as sustainable as possible, and to do that we saw the rotor blades as part of different research streams. We wanted to learn more about different recycling solutions, but also how we could avoid the blades going to landfill. “
When Vattenfall had to dismantle the Irene Vorrink wind farm in the Netherlands in 2022, the contractor had only one option: incineration. Vattenfall benefited from the extensive mapping it had done looking at the possibilities and options available on the market.
“As we had no other treatment methods within the contractor´s contract, it was up to us to direct the management of the blades to a third party. Gjenkraft, which was recently founded as a company, offered an interesting and promising recycling option we wanted to explore.”
Good timing made it an easy choice
In addition to the fact that Gjenkraft's research area was the recycling of composite materials, such as rotor blades, the timing was a crucial factor.
“For us, it was important to get a pipeline of blades from the dismantling project to the recycling company without it getting stuck on the way and needing to be temporarily stored. In this respect, our needs and Gjenkraft's research project fit together very well in terms of time”, says Gustav Frid.
Marcin Rusin, one of Gjenkraft's co-founders, says that the debate about wind turbine blades and how they could be recycled was the catalyst for the creation of the Norwegian recycling company. What started as a hobbyist project in the evenings for the co-founders is now a commercial business. It has received funding from Innovation Norway, The European Union, and other sources.
"Gjenkraft recycles composite waste to recover valuable materials in a sustainable and environmentally friendly manner. The goal is to do this in a 'green way' and not bury the waste in the ground or incinerate it for energy. Wind power has always been considered green energy, but there has been a challenge with the sustainable disposal of turbine blades when they reach the end-use time. And that's where we step in with our technology to make wind energy green again", he says.
Recycling valuable raw materials
Gjenkraft's method is a self-developed multi-step thermochemical process. It allows the recovery of glass and carbon fibers, as well as hydrocarbons in the form of gas and oil. The recycling company used carbon fiber to make skis in collaboration with Norwegian ski manufacturer Evi Ski.
"Our goal has always been to demonstrate that this challenge can be resolved. We already had the technology to recover valuable raw materials from composite waste, the next step was to find a high-end product that would appeal to the public. As a Norwegian company with team members who are enthusiastic about skiing, deciding to manufacture skis was a natural fit. We are very excited to see this concept come to fruition," adds Marcin Rusin, echoed by Gustav Frid:
“The important thing with the skis is to show the breadth of innovation. By showing the possibilities of using recycled materials, we can find new markets and applications.”
Legislation and incentives for more circular business
Regulations on the landfilling of composite materials, such as rotor blades, vary across the EU, with many countries still allowing it, but some, such as the Netherlands, prohibiting it.
In the future, Gustav Frid hopes that many more companies will try to use recycled materials in their manufacturing processes, but to become a reality, simpler legislation is needed.
“Today, for example, transport and circularity are on the table in the EU, where legislation and the high costs of transporting waste across borders create obstacles to effective recycling solutions. I hope there will be legislation and incentives that enable new circular businesses, so that new products with recycled content can establish themselves on the market.”
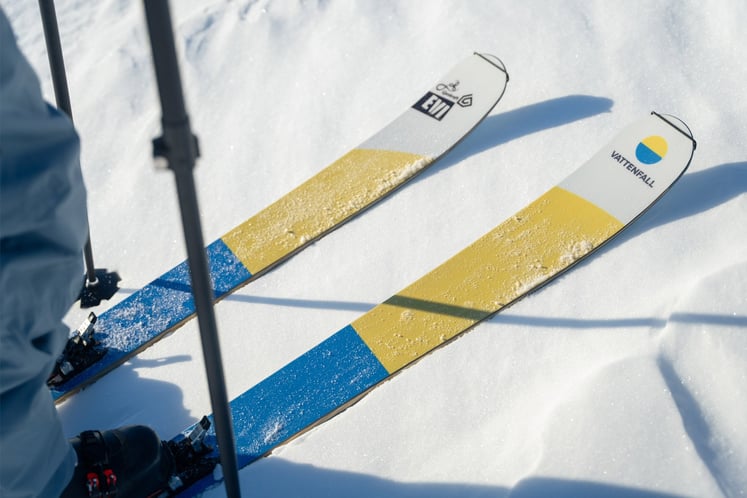
Discover the journey from blades to skis
Ever wondered how innovation can transform everyday materials into something extraordinary? Dive into our latest story and see how we turn wind turbine blades into high-performance skis.