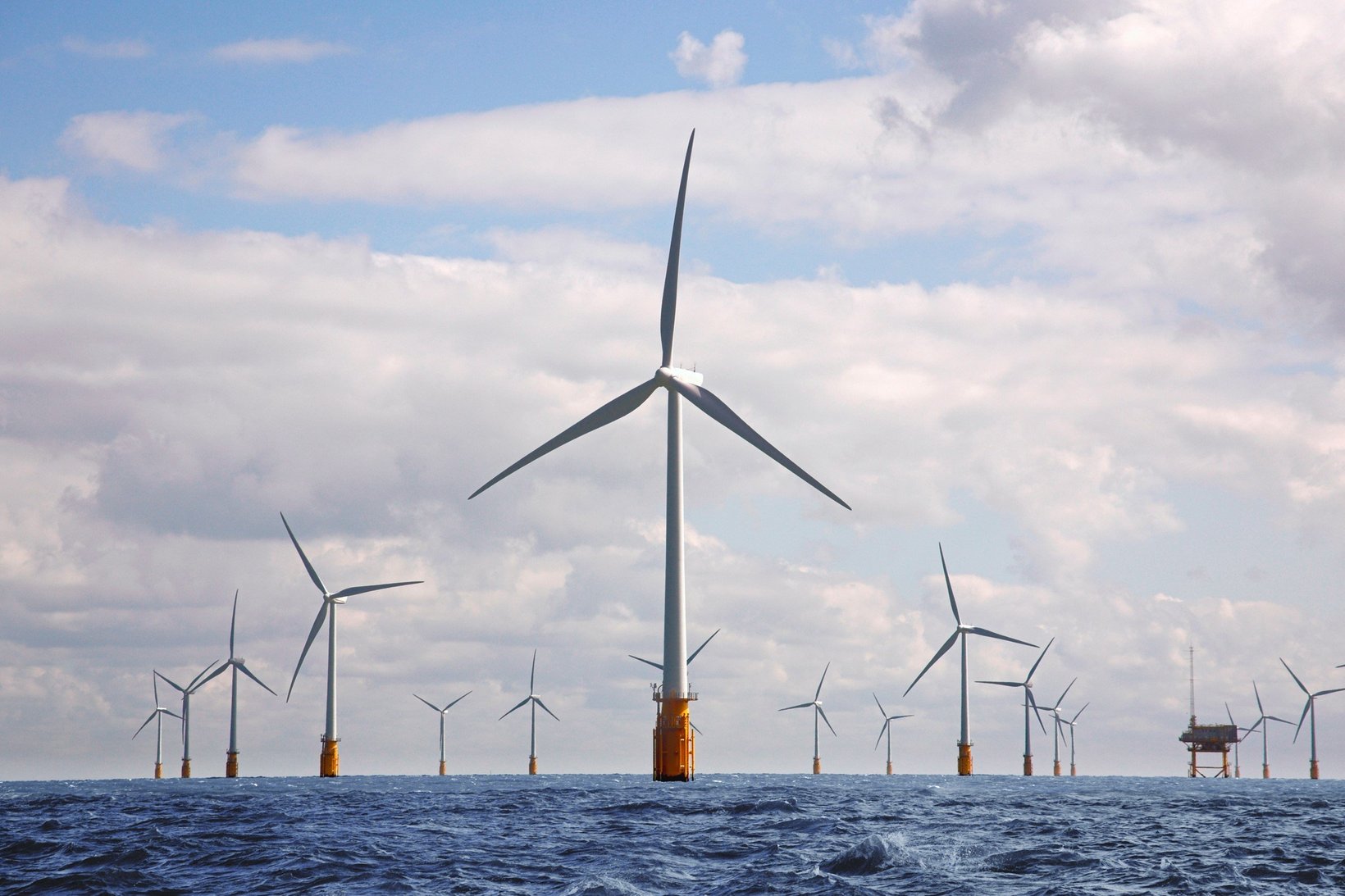
Cutting-Edge Process Turns Wind Turbine Blades into Reusable Materials
- A 44-metre long turbine blade from the Kentish Flats Offshore Wind Farm has been recycled for use in construction and manufacturing.
- This innovative approach keeps turbine components out of landfill.
A damaged turbine blade from Vattenfall’s Kentish Flats Offshore Wind Farm has been recycled by Northern Ireland based company, Plaswire. Plaswire has developed a sustainable solution which overcomes the challenge of what to do with scrap wind turbine components.
The recycling process will give new life to the old blade by turning it into RX Polymer, a material used for construction, packaging, furniture and logistics parts.
Being able to recycle old turbine blades within the UK is more environmentally friendly than sending them further afield, which can produce more carbon emissions as a result of the distances the old blade must travel to be processed.
Although 90% of a wind turbine is already recyclable, turbine blades are made of glass-fibre reinforced composite materials and are therefore more challenging to process. This year Vattenfall has expanded its ambitious targets to recycle all decommissioned turbine blades and other components by 2030.
Outside of the UK, Vattenfall has been exploring using old blades for construction, solar panel framing and as noise barriers. Most recently the concept of using blades as floating islands with space for housing and play areas was tested at Dutch Design Week.
Eva Julius-Philipp, Head of Environment and Sustainability at Vattenfall’s Business Area Wind, said:
“As the wind industry continues to grow to provide fossil-free energy across the globe, Vattenfall is committed to promoting a circular economy which reduces environmental impacts throughout the entire product lifecycle. Transforming decommissioned blades into new material is a crucial step in ensuring sustainable end of life solution for wind turbine components.”
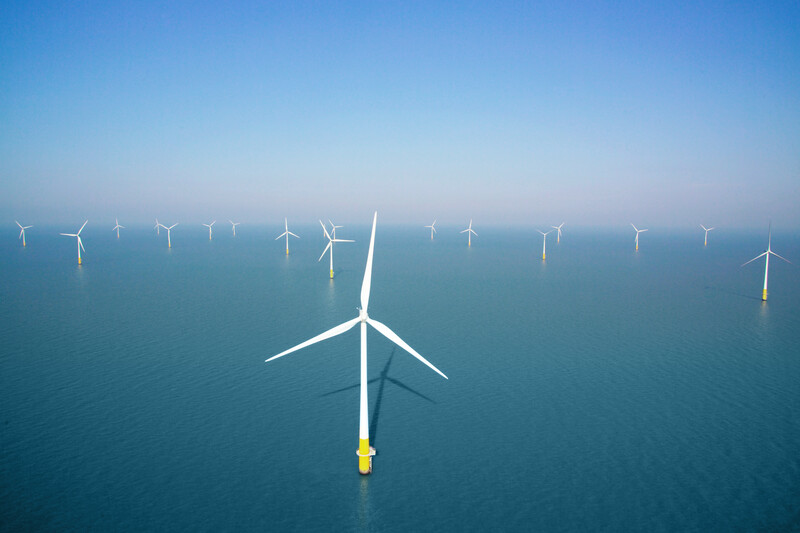
Notes to editors
Sending blades, permanent magnets, nacelle canopies and nose cones to landfill is already banned by Vattenfall, which operates 10 onshore and offshore wind farms in the UK. The company has also set a target of achieving 100% circular outflow of permanent magnets from their wind farms decommissioned from 2030 onwards, making Vattenfall one of the first developers to commit to a detailed circular economy target for these crucial components.
About the Kentish Flats Offshore Wind Farm
The Kentish Flats Offshore Wind Farm is one of five offshore wind farms built and operated by Vattenfall in the UK. Three of these, including Kentish Flats, are located off the coast of Kent, with all three producing enough electricity annually to power more than 400,000 UK homes. Since our first Kent wind farm – Kentish Flats – was built in 2005, offshore wind has become an affordable, reliable and vital part of the UK energy system.
About Plaswire
Plaswire creates commercial solutions for waste polymers within the industrial sustainability sector. Driven by innovation, Plaswire is deeply committed to the pursuit of a net-zero future where every action and decision is guided by the principles of environmental responsibility.
Smart systems and coded processing enables detailed Life Cycle Assessment (LCA) data for each blade, from its arrival for processing to the RX Polymer being produced, giving traceably and guidance for future recycling.
The RX Polymer solution diverts materials from incineration and cement kilns, preventing 2.7 tonnes of CO2 per tonne processed. RX Polymer products replace high virgin raw materials such as plastics and precast concrete and scarce wood, preventing additional carbon production.
In 2025 Plaswire will commission the first single pass blade processing line, located at a quayside close to an offshore wind farm, eliminating complex and expensive overland logistics.